\当サイトおすすめNo.1運行管理システム/
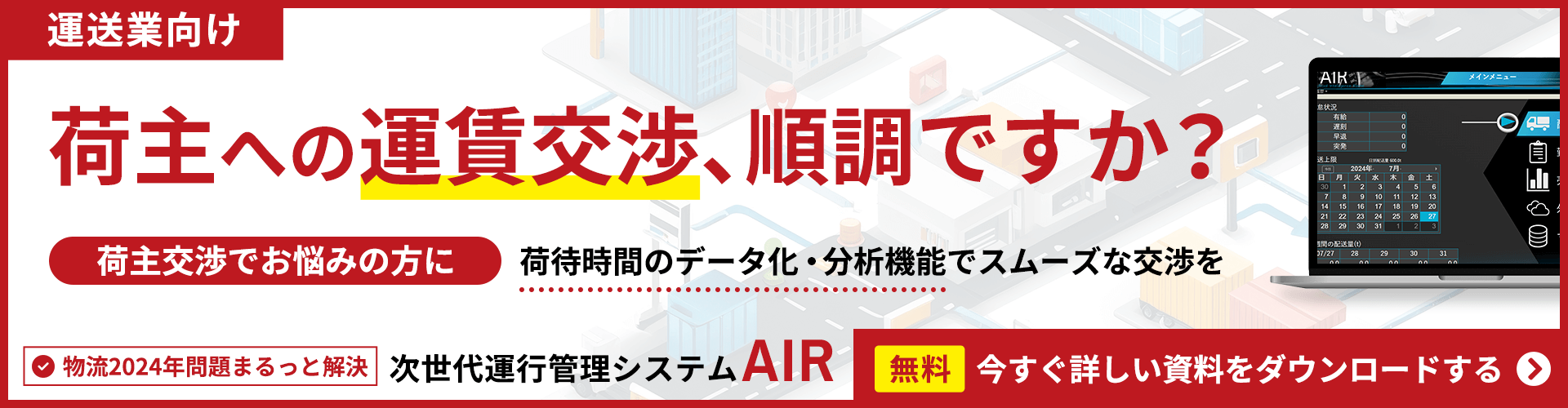
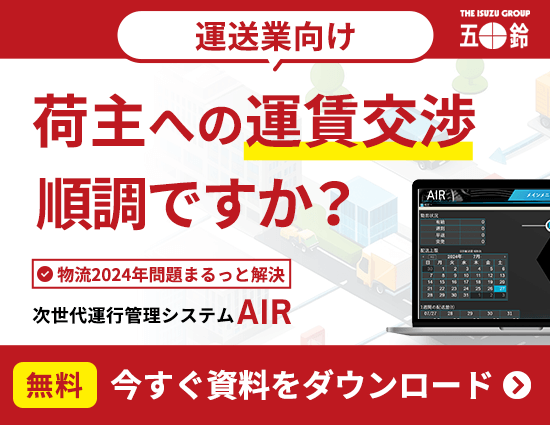
物流業界は近年、人手不足やコスト増加、2024年問題などさまざまな課題に直面しています。深刻な状況のなかでも企業の競争力を維持し、物流事業を存続させるには、物流業務の改善が必要不可欠です。
本記事では、物流改善の概要から具体的な課題点と解決策、さらに改善を支援するおすすめシステムや成功事例を解説します。
物流改善とは、以下の業務プロセスの効率性を高めながら無駄を削減する取り組みです。
輸送・入荷 | 商品が仕入先や生産拠点から倉庫へ運ばれ、受け入れる |
---|---|
入庫・保管 | 輸送された商品が倉庫に入庫し、適切な場所に保管される |
出荷(ピッキング・検品・梱包・流通加工) | 注文を受けた商品をピッキングし、検品・梱包・流通加工を経て出荷される |
配送 | 商品を配送する |
ここでは、物流の業務改善の基本的な考え方を解説します。
物流改善は、単に企業の利益を追求するだけではなく、荷主企業・顧客・従業員の3者すべてにメリットをもたらすことが重要です。
そのためコスト削減だけでなく、サービス品質の向上や作業者の負担軽減も同時に実現できることが、本質的な物流改善といえます。
たとえば、輸送ルートの見直しによってコストを抑えつつ、配送のスピードや正確さを向上させる施策が求められます。なお、以下の記事では配送計画の最適化について詳しく解説しています。
また、自動化やデジタル化を進めて作業者の負担を軽減することで、職場環境の改善にもつながります。結果として持続的かつ効率的な物流体制を構築でき、企業の競争力強化にも貢献します。
よって、物流改善を検討する際には効率性と働きやすさ、そして顧客満足度のバランスを取れるようにすることが最終目的となります。
物流改善を効果的に実現するためには、いくつかの重要な視点を持つことが必要です。ここでは、物流業務の効率化を図るうえで意識すべきポイントを解説します。
「3M(ムリ・ムダ・ムラ)」の排除を意識するようにします。
ムリは人員不足による過剰な業務負担、ムダは人的リソースの過剰配置や非効率な作業、ムラは品質や効率のばらつきを指します。
3Mを解消するためには、作業手順書の標準化や自動化・機械化などで業務の標準化に向けた取り組みを行うことが重要です。
現場で必要なスキルを明確にし、効果的な研修を実施することで、既存の人材に必要な能力を効率的に習得させることが可能です。個々のスキルレベルを把握し、適材適所の配置を徹底することで、生産性を最大化できるでしょう。
物流コストの削減において、人員配置の最適化も重要です。
出荷量の変動に関わらず固定人員を配置したり、繁忙と閑散の差を考えずに一定数のスタッフを配置したりすると、無駄な人件費が発生するため、需要に応じて柔軟に配置できる体制を構築することが理想的です。
作業工程を適切に管理するためには、作業記録を詳細かつ正確に把握することが不可欠です。そのためには、デジタル化やシステム化の積極的な推進が求められます。
従来の手書き報告書による管理では記入ミスや情報共有の遅延が発生しがちでしたが、報告書や日報などをデジタル化することで作業の進捗状況や品質データを即時に共有できれば、問題の早期発見と迅速な対応が可能になります。
物流改善の方法によっては、荷主企業の協力なくしてはなしえない内容があります。
特に、ドライバーの拘束時間や物流コストの削減に取り組む際には、多くの場合に荷主との連携が欠かせません。具体的には、以下のような改善方法が該当します。
改善方法 | 具体例 |
---|---|
発着時間の変更 | ・配送時間を分散させることで、ピーク時の混雑や待機時間を削減 ・柔軟な納品時間を許容してもらうことで、ドライバーの負担が軽減 |
付帯業務内容の変更 | ・検品や荷下ろし作業を効率化するため、自動化設備の導入や作業分担を見直し ・荷主側での検品を強化することで、現場での滞留時間を短縮 |
運送委託の見直し | ・共同配送や積載率の向上を図ることで、物流コストを削減 ・契約条件を柔軟に変更し、運行効率を向上させる取り組みを促進 |
発着時間や付帯業務内容の見直しはドライバーの拘束時間の削減などに効果的ですが、荷主側の柔軟な対応が求められるため、相互理解を深めた協力体制の構築が重要となります。
厚生労働省の「荷主のための物流改善パンフレット」では、荷主企業に向けた案内が網羅されていますので、そちらを案内することも有効です。また、荷主企業との協力体制の構築には、後の章の成功事例でも触れていますのでケースごとに参考にしてください。
ここでは運送事業者側で行える、物流改善の具体的な方法を業務プロセス別に解説します。
輸送と入荷の効率化は、コスト削減と納期短縮に直結します。以下で輸送・入荷の具体的な改善方法を紹介します。
トラック輸送だけでも、以下のような選択肢が存在します。それぞれのメリットにあわせて選ぶことで、効率的な輸送によるコスト削減を狙うことが可能です。
トラック輸送の主な種類 | メリット |
---|---|
路線便 | 小口配送に適し、コストを抑えやすい |
チャーター便 | 時間指定が厳しい場合に有効 |
共同配送 | 複数企業がトラックをシェアし、環境負荷とコスト削減を両立 |
共同配送について詳しく知りたい方は、以下の記事をご覧ください。
予約受付システムの導入によって、トラックの到着が重なることで発生する混雑や滞留を防ぎ、スムーズな入荷処理が実現できます。
配送車両の到着時間を事前に調整・管理できるため、待機時間を短縮でき、ドライバーの拘束時間が減少することで、労働環境の改善にもつなげることが可能です。以下の記事では、予約受付システムについてより詳しく解説しています。
拠点が多すぎると拠点間輸送のコストは膨らみますが、適切に配置すれば配送リードタイム短縮などの利点も得られます。自社の出荷量や配送エリアを客観的に分析し、最適な拠点戦略を立てることが重要です。
モーダルシフトなどの輸送方式の変更は、トラック輸送(陸路)を、環境負荷が少なく大量輸送が可能な鉄道や船舶(海運)に切り替える取り組みのことです。
長距離輸送を鉄道・船に任せることで、ドライバーの拘束時間や人員負担を減少させる効果が見込めます。
倉庫管理システム(WMS)により、在庫の見える化や作業の効率化を実現し、入出庫作業のミス削減や保管スペースの最適化が可能になります。
TMS(輸配送管理システム)やERPシステムと連携させることで、物流全体の一元管理も実現します。
棚卸作業を自動化することで、作業効率や在庫管理精度が飛躍的に向上し、人的ミスを大幅に削減できます。棚卸作業を自動化する主な方法は、以下のとおりです。
作業例 | |
---|---|
RFID(無線ICタグ)の活用 | 商品にRFIDタグを貼り付け、専用リーダーで一括スキャンする |
自動棚卸ロボットの導入 | 倉庫内をロボットが自動走行しながら在庫をスキャンする |
ピッキングシステム導入により、作業効率の向上や作業ミスの削減、教育コストの削減など幅広い効果が期待できます。また、ロボットピッキングシステムでピッキング作業そのものを自動化する場合には、人材不足に強力に対処することも可能です。
主なピッキングシステムの種類として、以下のようなものが挙げられます。
デジタルピッキングシステム | 棚に設置したデジタル表示器が点灯し、指示通りに商品をピッキング |
---|---|
音声認識ピッキングシステム | 音声ガイドに従ったピッキングを実施する |
ロボットピッキングシステム | 自動ロボットが商品を直接取り出してピッキングする |
作業効率を上げるためには、フォークリフトやピッキングカート、コンベアといったマテハン機器の活用が効果的です。
さらに、人力作業をシステムや機械による自動化・省力化に置き換えることで、人為的ミスの削減と作業速度向上の両立が可能となります。
エラーが発生しやすい工程では、バーコードスキャナー付きハンディターミナルを活用することが有効です。
小さなミスの防止策が全体の業務効率向上につながることを理解し、継続的な改善に取り組むことが重要です。
配送ルートの最適化はシステムやツールの利用などのデジタル化が注目を集めています。
なかでもシステムで無駄な走行や待機時間を削減することで、燃料費や人件費の削減に直結し、配送効率と顧客満足度の向上が期待できます。配送ルートの最適化の一般的な方法は、以下のとおりです。
配送管理システムの導入 | 配送ルートを自動計算し、ルート変更にも柔軟に対応 |
---|---|
運行スケジュールのデジタル化 | エクセルなどで配車計画をデジタル化 |
システムで配送ルートの最適化を目指す場合には、自社の課題にあわせたシステムの選定が重要です。
システムで配送計画を自動作成することで、配車業務の標準化や作業負担の軽減、コスト削減、業務効率の向上などを実現します。
配送計画を自動作成する具体的な方法には、自動配車システムの活用が有効です。自動配車システムは、AIやアルゴリズムを活用して最適な配送ルートや車両割り当てを自動で計算し、リアルタイムで交通状況や荷量を考慮して配車計画を立案します。
これにより、人手による配車ミスを防ぎ、効率的な運行管理が可能となります。
ここでは、物流の改善におすすめのシステムを紹介します。以下は主要サービス3つの比較表です。
サービス名 | トータル物流基幹システムAIR 詳細を確認する | Loogia 詳細を確認する | Air Logi 詳細を確認する |
---|---|---|---|
自動配車機能の有無 | |||
操作性 | 直観的な操作しやすさに配慮された操作画面 | 直感的なインターフェース | 条件や数値の入力が容易 |
労務管理連携 | 公式サイトに情報なし | ||
特徴 | 物流業務全体を見える化し、一元管理 受注から配車、運行管理に対応 運転日報の自動作成が可能(ドライバー用アプリが使用可能) | 配車条件の詳細設定 注文情報のデータ入力 VICS統計情報を用いた高精度な配車計画の策定 | 高頻度なアップデート 配送先別に仕分ける作業をサポートする独自機能 充実したサポート |
トータル物流基幹システムAIRは、物流業務のあらゆる工程を一元管理できるクラウド型システムです。受注管理から配車計画、運転日報の作成、請求・仕入業務まで、物流オペレーション全体を管理できます。
さらに、営業所間の情報共有機能によって、帰り便の活用や複数荷物の積みあわせ配送など、コスト削減と環境負荷軽減を両立する物流体制の構築が可能になります。
主要機能 | ・運転手の労務管理や運転日報登録 ・最適な経路を自動計算する自動配車機能搭載 ・業務の見える化で業務効率化に大きく貢献 ・クラウドベースのシステムで導入時の負担を軽減 ・配車連携機能で複雑な条件下での配車にも対応 |
---|---|
所在地 | 東京都千代田区丸の内2-2-1 岸本ビル |
価格・料金プラン | こちらからお問い合わせできます |
Loogiaは、配送業務の効率化を支援する配車・動態管理システムです。
運用面では、各車両のGPS位置情報や配送進捗状況を確認できるため、予定時刻からの遅延発生時にも迅速な対応が可能です。
主要機能 | ・配車条件の詳細設定・注文情報のデータ入力・VICS統計情報を用いた高精度な配車計画の策定 |
---|---|
所在地 | 東京都目黒区下目黒1-7-1 パスコ目黒さくらビル |
価格・料金プラン | ・パブリッククラウド版初期設定費用:30万円月額費用:4万8千円/1ライセンス ・スタンドアロン版アプリケーション利用料:300万円月額費用:4万円/1ライセンス ・イントラ初期費用:500万円月額費用:5万円/1ライセンス |
Air Logiは、実績豊富なクラウド倉庫管理システムです。
開発・提供元のコマースロボティクスには、多数の物流技術管理士が在籍しています。現場で培われたノウハウを活かしたカスタマイズ提案とサポートが受けられる点も大きな強みです。
主要機能 | 帳票出力の効率化庫内移動距離削減機能を搭載ピッキング作業の効率化 |
---|---|
所在地 | 〒105-0021東京都港区東新橋2-11-4 マヤパダ汐留プラザ5F |
価格・料金プラン | 3PLプラン初期費用:3万5,000円(初回ショップのみ、21日間の無料トライアルあり)月額利用料:1万円~ ショッププラン初期費用:3万5,000円(21日間の無料トライアルあり)月額利用料:3万円~ ※両プラン共通導入支援:要お問い合わせハンディ費用(オプション):スマホハンディは初期/月額それぞれ6,500円/台 ※キーエンス製は要問合せ |
鶴信運輸株式会社では、ドライバーの長時間拘束が問題視されていました。特に、積み下ろし作業や荷待ち時間が長時間労働の主な要因となっており、効率的な運行管理が求められていました。
これらの解決方法として、スワップボディコンテナ車両を導入し、荷役分離を実現しました。荷役作業と配送作業を分担し、ドライバーが積み下ろしを待機する必要がなくなり、拘束時間が大幅に削減されました。
コンテナの着脱も20分程度で完了するため、作業効率が飛躍的に向上し、片道便の改善と長距離ルートの見直しにもつながっています。
これにより、長距離運行の負担が軽減し、ドライバーの労働時間を適正化することができました。
菱木運送株式会社ではドライバーの休息が十分に取れていないケースがあり、改善基準告示の遵守が難しい状況が続いていました。そこで運行時間をリアルタイムで可視化できる独自システムを導入しました。
ドライバーが自ら時間管理を意識するようになり、過労運転のリスクが低減されました。また、運転者ごとの勤務データを一元管理することで、特定ルートやドライバーに負担が偏らないよう業務を調整し、業務の平準化にもつながっています。
さらに、システムで得た運転情報を荷主企業にも共有することで、労働時間や荷待ち時間の実態を可視化しました。結果として、荷待ち時間の短縮や積み下ろし方法の見直しも実現しています。
ある物流倉庫では発荷主(工場)側の在庫管理や出荷場の狭さが原因で、工場敷地内でトラックの長時間待機が発生していました。これに対し、外部倉庫の活用と入退場・進捗管理システムの導入を実施しました。
出荷貨物の状態をリアルタイムで把握できることで、工場内スペース不足による生産遅れが解消されました。
また、運転手の出勤時間を調整し、待機なしでスムーズに入構できる体制を構築したことで、入構から出構までの待機時間が平均26分短縮し、出勤から入構までの時間も90分短縮しました。
さらに、運行状況データを荷主企業とも共有し、情報の透明化により協力体制を強化することで、荷待ち時間やバラ積み作業の改善にも成功しています。
ある紙製品製造業では、出荷台数が多すぎて着荷主側の荷役スペースを圧迫し、待機時間が発生する問題がありました。特に、着荷主側の荷役スペースが狭く、最大でも3台同時にしか荷卸しができないため、入荷が集中すると処理が滞る状況でした。
この課題を解決するため、着荷主側の処理能力を事前に把握し、発荷主側の出荷台数を1日10台に抑制しました。
これにより、入荷量が平準化され、荷役作業がスムーズに進行し、待機時間が大幅に削減されました。発荷主と着荷主の相互理解を深めた調整が、スムーズな物流改善に寄与した成功事例です。
物流業務の改善は、人的ミスの排除・コスト適正化・業務全体の見える化といった視点から総合的に取り組むことが重要です。
このような改善策を実践することで、物流品質の向上とコスト削減の両立、さらに顧客満足度の向上などのメリットの享受が可能になります。
企業間物流に詳しい!運行管理のプロ監修「運行管理ナビ」編集部です。